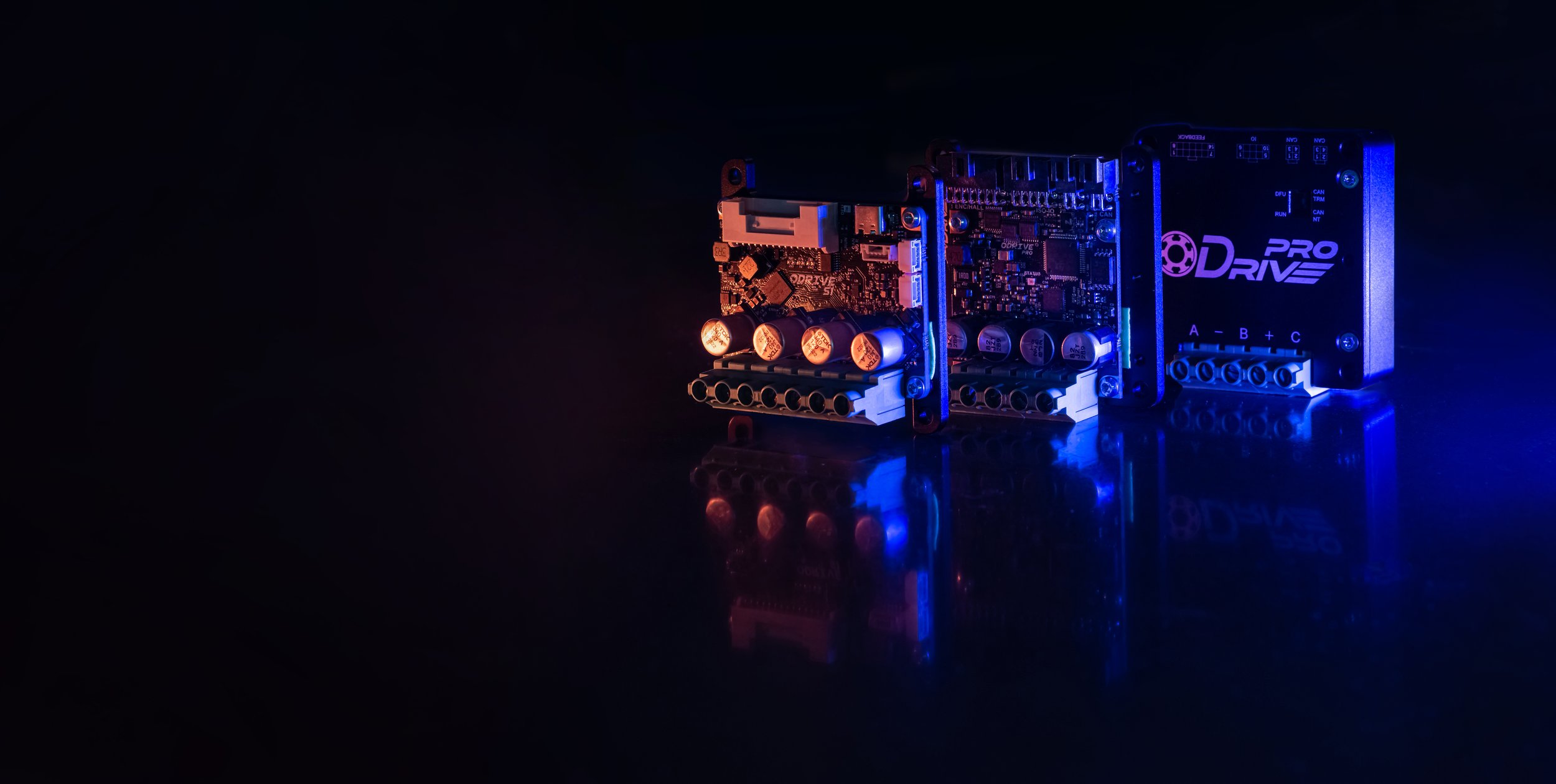
ODrive Pro
The benchmark in precision motor control. Engineered for power, robustness, and versatility, ODrive Pro sets a new standard, designed to meet the rigorous demands of advanced robot applications.
3000W Continuous Power - 5 kW peak, 14-58V including 14S batteries, with regenerative braking.
Precision Control - Torque, Velocity, Position & Trajectory control, with model based feed-forward.
Ground-up Reliability - Locking connectors, extensively tested power stage, anti-vibration electrolytic capacitors.
Robust Feedback - Differential absolute encoder interface: noise immunity and instant cold starts. Dual encoder support. Filtered incremental and Hall feedback with common mode immunity.
Isolated IO - Galvanically Isolated CAN, UART, Step/Direction and GPIO.
User Interface: Web GUI & Python tools for easy configuration.
Easy Integration - With Python, Arduino, CAN, and ROS2 libraries available.
High Density - 51 x 64 mm footprint, on-board magnet encoder IC.
Proven Reliability - Thousands of units in the field.
ODrive S1
With a focus on core functionality, the ODrive S1 delivers unprecedented value to an integrated robot system. Supporting our new generation of firmware, software, and algorithms, the S1 is designed for versatility, and efficiency. For those new to the ODrive ecosystem, or looking for a smooth transition from ODrive v3.6, the S1 offers a solid solution for advanced motor control.
1600W Continuous Power - Supporting 12-50V Input, including 12S Batteries, with regenerative braking or brake chopper.
Brake Chopper - Safely handle 2000W peak regenerated power with external brake resistor.
Precision Control - Torque, Velocity, Position & Trajectory control, with model based feed-forward.
Encoder Support - RS485, SPI and on-board absolute encoders allow instant cold starts. Dual encoder support. Filtered incremental and Hall feedback.
Isolated IO - Galvanically Isolated UART, Step/Direction and GPIO.
CAN - Designed for many-axis CAN network, with daisy-chain connectors.
User Interface: Web GUI & Python tools for easy configuration.
Easy Integration - With Python, Arduino, CAN, and ROS2 libraries available.
Compact Design - 66 x 50 mm footprint, all-in-one locking connector.
Web GUI
Configure and tune the ODrive Pro or S1 effortlessly directly from your browser, works on any OS.
Instant launch - No software or driver installation required.
Quick setup - Intuitive wizard takes you through the setup process.
Control at your fingertips - Jog, plot and tune one or multiple axes at once.
Advanced Tweaks - Access hundreds of parameters in an organized tree view.
Complete System
Easy Integration - With Python, Arduino, CAN, and ROS2 libraries available.
User Interface: Web GUI & Python tools for easy configuration.
Encoder Support - RS845, SPI and on-board absolute encoders allow instant cold starts. Dual encoder support. Filtered incremental and Hall feedback.
CAN - Designed for many-axis CAN network, with daisy-chain connectors.
Isolated IO - Galvanically Isolated UART, Step/Direction, PWM and GPIO.
Motion control
Advanced motion control with FOC at the core.
Closed Loop - feedback control, with support for dual encoders.
Field Oriented Control - Smooth and precise current control.
Diverse Control Modes - Torque, Velocity, Position, Trajectory and Filtered input and control modes.
Model Feed Forward - Control action before error builds up.
System Identification - Measure resistance, inductance, and encoder alignment automatically.
Anti-cogging - Upgrade motor smoothness with cogging torque mapping.
Optimal Estimator - Accurate velocity from discrete feedback.
Reliability - robustness
Voltage Limits - Enforce voltage levels to protect system components.
Power Limiting - Motor torque, speed and current limits to prevent system overloads.
Thermal Protection - Real-time monitoring of both ODrive and motor temperatures with automatic thermal foldback.
Fault Detection - Ensures operational safety by identifying faults and promptly de-energizing the motor.
Tools - support
Documentation - Guides, hardware specifications, product manual, and articles.
Python Library - Configuration, control, and plotting with Python.
Arduino Library - Easy to use ODrive commands in your Arduino sketch.
ROS CAN Package - Tools to integrate ODrive into a ROS and CAN based robot controller.
Get Support - Ask questions on our Forum or Discord, or contact us.
Customizations - Need a firmware feature or integration support? Contact us.